Manufacturing businesses operate in a unique environment where financial clarity and process efficiency are critical for success. Unlike service-based companies or retailers, manufacturers must navigate complex cost structures involving materials, labor, overhead, and inventory. To ensure profitability and sustainability, it’s essential to maintain accurate records, understand your cost drivers, and employ the right accounting methods.
This guide walks you through the foundational elements of manufacturing accounting, outlines how cost components are calculated, explores costing methods, and explains the role of inventory valuation. It also highlights the importance of using specialized software to streamline your accounting processes, improve decision-making, and reduce operational waste.
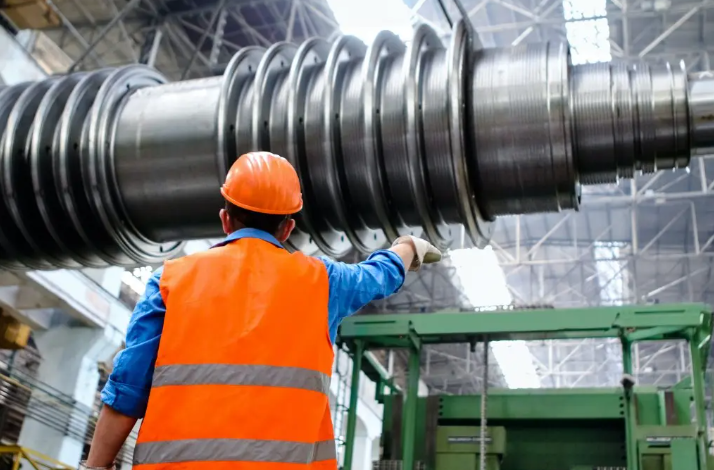
Why Accounting Matters in Manufacturing
In a competitive market, manufacturers must constantly assess how efficiently they convert raw materials into finished goods. Keeping a close eye on the financial impact of each step in production helps reduce inefficiencies, minimize waste, and improve profit margins.
Whether you’re running a small fabrication shop or a large-scale factory, accounting systems allow you to track every dollar spent—on materials, labor, machinery, utilities, and storage—and evaluate how these costs influence pricing, profitability, and resource allocation.
Accurate accounting doesn’t just support compliance and financial reporting; it forms the backbone of strategic business decisions. Manufacturers that successfully integrate financial insights into daily operations are better positioned to adapt to market fluctuations, manage cash flow, and plan for growth.
Breaking Down Manufacturing Costs
Before you can optimize your production operations, you need a firm grasp of the different types of costs involved in manufacturing. These costs can be categorized into direct and indirect components that collectively form your product’s total cost.
Direct Materials
These are the raw inputs that are physically incorporated into the final product. For instance, if you manufacture wooden furniture, your direct materials include wood, nails, glue, and finishes. The cost of these materials is calculated based on purchase price and consumption rate, typically outlined in a bill of materials (BOM).
In process-driven industries like chemical production or food processing, the BOM may resemble a recipe, specifying ingredient quantities and ratios required for a single batch.
Direct Labor
Direct labor costs reflect the wages, salaries, and benefits paid to workers directly involved in the production process. These can include assembly line operators, welders, machinists, and other skilled personnel. Time tracking and payroll records are essential for determining this figure, especially when overtime or shift differentials are involved.
Indirect Manufacturing Costs
Also known as manufacturing overhead, these include expenses not directly tied to a specific product but necessary to keep the factory running. Examples include factory rent, equipment depreciation, maintenance, utilities, supervisory staff wages, and safety supplies. Allocating overhead accurately is vital for true cost assessment.
Work in Progress (WIP)
Products that are partially completed at any point in time represent WIP inventory. These items have incurred some combination of material, labor, and overhead costs, but are not yet ready for sale. WIP values fluctuate based on production schedules and must be tracked regularly to gauge operational efficiency.
Finished Goods
Once production is complete, items move into finished goods inventory. These are ready for sale and include all accumulated costs, from raw material usage to storage and packaging. Maintaining an accurate valuation of finished goods is essential for setting prices and assessing profitability.
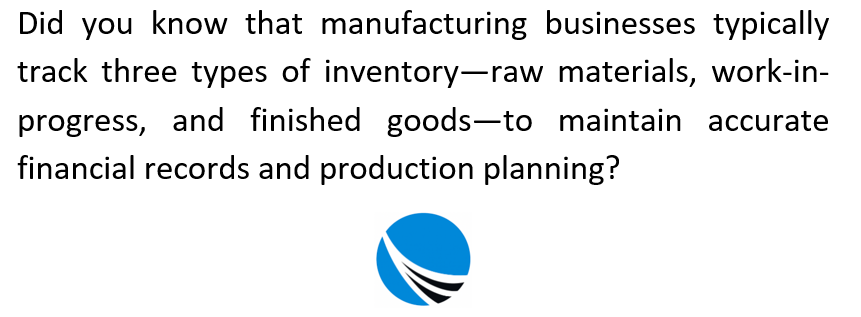
Choosing the Right Costing Method
Selecting a suitable costing approach enables you to price products competitively, evaluate profitability, and make informed business decisions. Manufacturing operations can employ several costing techniques depending on their production structure and objectives.
Standard Costing
Standard costing involves assigning a predetermined cost to materials, labor, and overhead for each unit produced. These benchmarks are based on historical data, market rates, and productivity estimates.
The key advantage of standard costing is its ability to identify variances—differences between expected and actual costs. Regular variance analysis helps pinpoint inefficiencies and guide corrective actions. This method is ideal for businesses that produce high volumes of similar goods, where consistency and efficiency are critical.
Job Order Costing
In contrast to standard costing, job order costing calculates expenses for each custom production job or batch. It tracks specific inputs and labor associated with individual projects. This method is especially useful for manufacturers of specialized machinery, prototypes, or custom furniture, where costs vary significantly between orders.
Job costing provides granular visibility and helps businesses determine appropriate markups to achieve target margins. It’s widely used in industries like construction, aerospace, and bespoke manufacturing.
Activity-Based Costing (ABC)
ABC allocates indirect costs based on specific activities that contribute to production. Instead of using a blanket rate for overhead, this method ties expenses to actions such as machine setup, quality control, or material handling.
ABC offers a more accurate picture of product-level profitability and is beneficial for manufacturers with diverse product lines or complex processes. By revealing which products consume the most resources, it helps prioritize efficiency improvements and product mix optimization.
Inventory Valuation: Assessing Your Stock’s Worth
Inventory valuation plays a crucial role in financial reporting and cost management. It determines how much your unsold inventory is worth at the end of an accounting period, which in turn affects your cost of goods sold (COGS), profit margins, and tax obligations.
Manufacturers can adopt several inventory valuation methods, each with different implications for financial results and tax strategy.
First-In, First-Out (FIFO)
Under FIFO, the earliest goods purchased are the first to be used or sold. This method aligns with the natural flow of inventory and is particularly useful when dealing with perishable items or goods with expiration dates. During inflation, FIFO generally results in lower COGS and higher net income.
Last-In, First-Out (LIFO)
LIFO assumes the most recently acquired inventory is sold first. Though not widely used outside of certain jurisdictions (and not permitted under IFRS), it can be advantageous in periods of rising costs, as it leads to higher COGS and lower taxable income.
Weighted Average Cost
This method calculates a moving average cost per unit by dividing the total cost of goods available for sale by the number of units. It’s simple to apply and suitable when goods are indistinguishable from one another. It smooths out price fluctuations and is commonly used in bulk production environments.
Specific Identification
Specific identification tracks the cost of individual items, using serial numbers or barcodes to link expenses to specific units. It offers the most precision but is typically reserved for high-value or unique items, such as luxury vehicles or custom electronics.
Why Inventory Management Matters
Effective inventory control is essential for maintaining balance between supply and demand. Overstocking ties up capital and storage space, while understocking can result in missed sales and customer dissatisfaction.
Accounting systems should support real-time inventory tracking and integrate seamlessly with purchasing and sales modules. A robust inventory management process ensures that WIP, raw materials, and finished goods are accurately recorded and valued, reducing discrepancies and enabling better forecasting.
Whether using a periodic system (evaluating inventory at set intervals) or a perpetual system (updating inventory levels continuously), having a clear understanding of stock levels is vital for avoiding costly mistakes.
Features to Look For in Accounting Software for Manufacturers
Manual accounting methods are time-consuming and error-prone, particularly as your operations grow. The right software can simplify your workflows, automate repetitive tasks, and provide real-time insights that empower smarter decisions.
Here’s what to consider when choosing an accounting solution tailored to manufacturing:
Real-Time Cost Tracking
Your software should automatically record material usage, labor hours, and overhead, assigning them accurately to jobs or products. This allows for timely analysis of production costs and profitability.
Inventory Integration
A strong accounting platform should link directly with inventory systems, providing visibility into stock movements, reorder points, and obsolescence. Features like automatic alerts and replenishment planning can reduce shortages and excess.
Customizable Reporting
Look for systems that allow you to generate detailed reports on cost variances, profit margins, and production efficiency. Flexible reporting tools help you track key performance indicators (KPIs) and support continuous improvement.
Scalability
Choose a solution that grows with your business. As your operations become more complex, your system should support additional features like multiple warehouses, product lines, or international compliance requirements.
Compliance and Tax Management
Your software should help you stay compliant with tax regulations, financial reporting standards, and industry-specific laws. Built-in audit trails, secure access controls, and regular updates are essential for protecting your data and reputation.
Integration with ERP
Many manufacturers benefit from using Enterprise Resource Planning (ERP) systems, which consolidate accounting, production planning, procurement, and human resources. A fully integrated solution ensures that departments work from the same data source, improving collaboration and decision-making.
Conclusion: Building a Strong Financial Foundation
Manufacturing accounting is more than just bookkeeping—it’s a vital management tool that influences pricing, production planning, and profitability. By understanding cost structures, choosing the right valuation and costing methods, and investing in specialized software, manufacturers can position themselves for long-term success.
Accurate, timely financial information supports better resource allocation, highlights inefficiencies, and enables faster response to market demands. Whether you’re streamlining your shop floor or scaling your operations, strong accounting practices are key to making smarter business decisions and achieving sustainable growth.
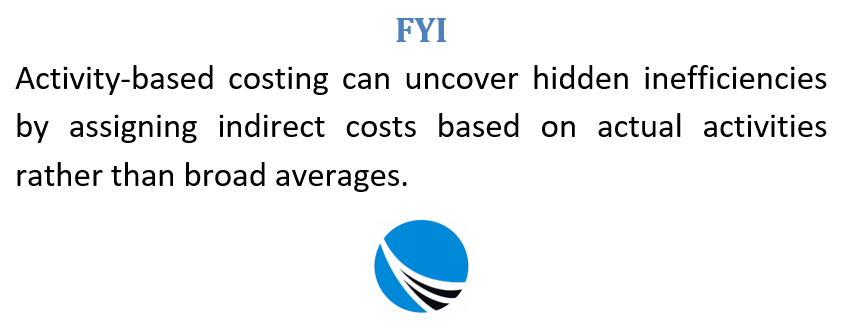
FAQs about Manufacturing Accounting
What Makes Manufacturing Accounting Different From Other Types?
Manufacturing accounting includes tracking direct materials, labor, and overhead costs, as well as managing work-in-progress and finished goods inventory—making it more complex than retail or service accounting.
Why Is Accurate Cost Tracking Important?
It helps determine product pricing, assess profitability, reduce waste, and support informed decision-making in production and business strategy.
What Are Direct Material Costs?
These are the raw materials used directly in the production of goods, such as metal, fabric, or chemicals depending on the industry.
What Are Direct Labor Costs?
Direct labor costs include wages, benefits, and payroll taxes paid to employees who are directly involved in manufacturing the product.
What Is Manufacturing Overhead?
Overhead refers to indirect production costs like equipment maintenance, factory utilities, and supervisory salaries that support the production process.
Why Is Inventory Valuation Essential?
It ensures accurate financial reporting, determines cost of goods sold, and helps track profitability and operational efficiency.
What Is Standard Costing?
Standard costing assigns predetermined costs to materials and labor, enabling variance analysis to identify inefficiencies or pricing adjustments.
When Should Job Order Costing Be Used?
It’s ideal for custom or small-batch manufacturing, allowing businesses to track specific costs for each unique product or client order.
What Is Activity-Based Costing?
ABC assigns costs based on actual activities and resource consumption, making it suitable for complex operations with varied product lines.
Which Inventory Valuation Method Is Best?
The choice depends on business needs: FIFO is common for perishable goods, LIFO may reduce taxes during inflation, and average costing simplifies tracking.
How Does Software Improve Manufacturing Accounting?
It automates cost tracking, integrates inventory, enhances reporting, supports compliance, and enables real-time decision-making across departments.